Research Themes
MATERIALS FOR ADDITIVE MANUFACTURING
- New material development
- Materials/Powders characterization
- Process development and optimization
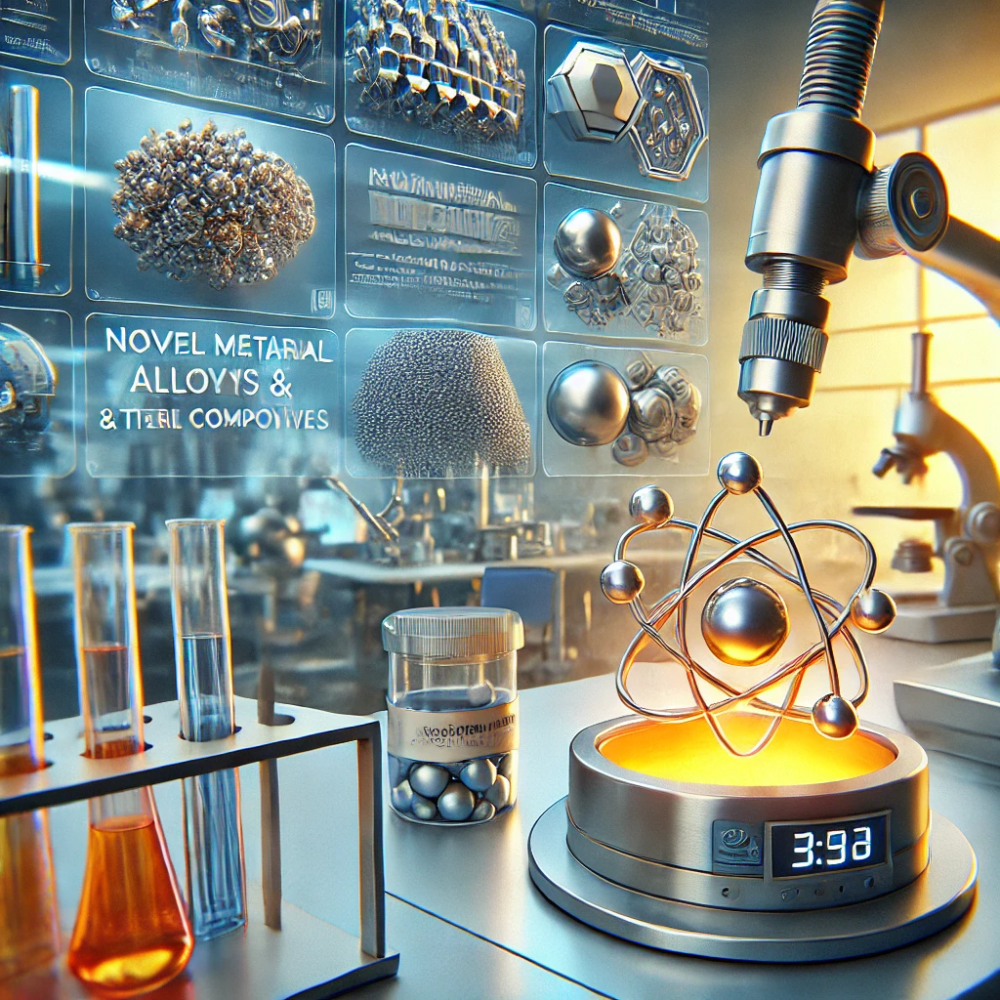
Materials and Process
New Material Development: This theme is dedicated to the innovation and development of novel materials tailored for LPBF and binder jetting. The focus is on creating advanced metal alloys, functional materials and composite materials that offer superior mechanical properties, enhanced thermal stability, and improved corrosion resistance. These developments aim to broaden the application scope of additive manufacturing, meeting the stringent requirements of high-performance industries such as energy, aerospace, automotive, and biomedical engineering.
Materials/Powders Characterization: In-depth characterization of powders used in LPBF and binder jetting is critical. Advanced techniques such as Scanning Electron Microscopy (SEM), X-ray Diffraction (XRD), and thermal analysis are employed to assess particle size distribution, morphology, flowability, and thermal properties. This comprehensive analysis ensures the reliability, performance, and quality of the final additive manufacturing products.
Process Development and Optimization: This research theme focuses on refining and enhancing the precision of Laser Powder Bed Fusion (LPBF) and binder jetting techniques. By optimizing laser parameters, powder characteristics, and environmental conditions, we aim to minimize defects, improve build rates, and ensure the structural integrity of manufactured parts. This includes the integration of real-time monitoring systems for superior process control.
DESIGN FOR ADDITIVE MANUFACTURING
- Design Guidelines for AM
- Multi-Physics Multi-Objectives Topology Optimization
- Lattice Structures
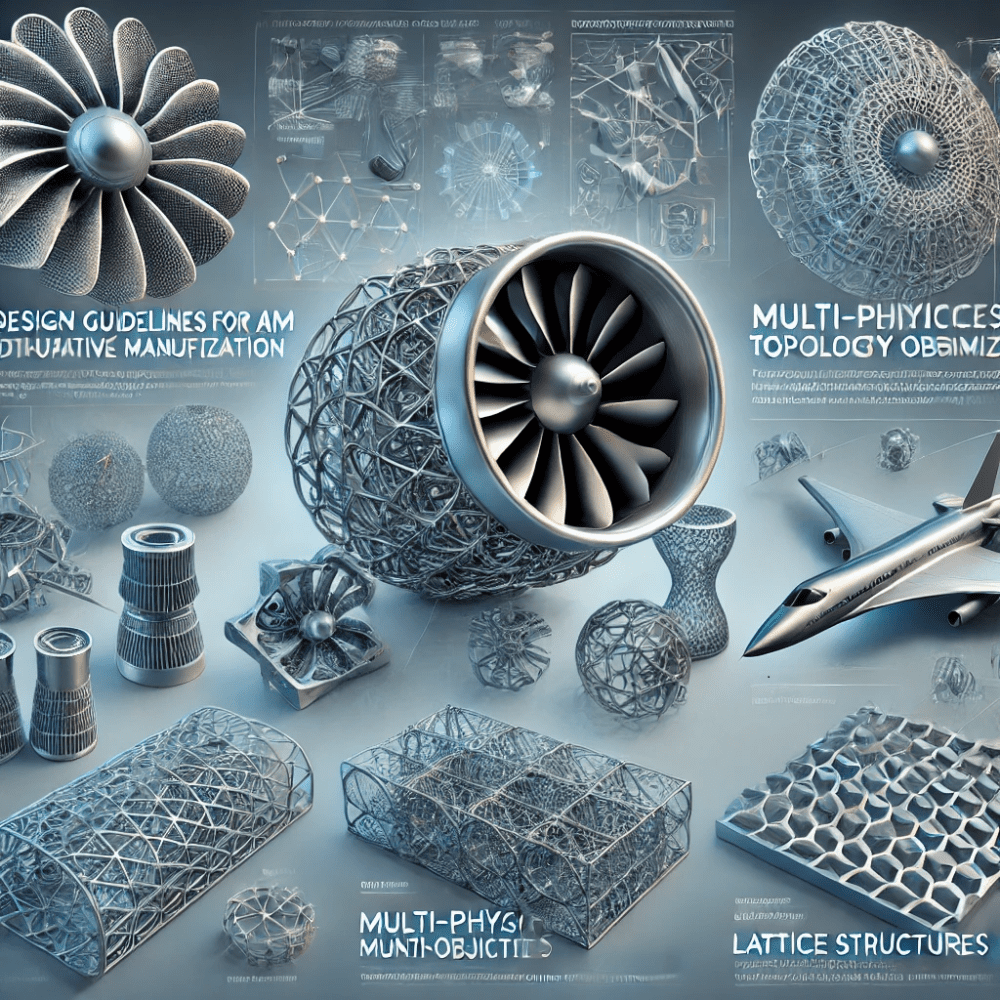
Design for AM
Design Guidelines for AM: This theme focuses on developing comprehensive design guidelines tailored for additive manufacturing (AM). These guidelines address the unique capabilities and limitations of AM technologies, such as layer-by-layer construction and material deposition. By understanding and leveraging these aspects, designers can create optimized parts that are not only manufacturable but also exhibit enhanced performance and efficiency. The guidelines cover various industries including energy, automotive, aerospace, and biomedical, ensuring that designs meet the specific requirements of each field.
Multi-Physics Multi-Objectives Topology Optimization: Research in this area aims to advance the use of multi-physics and multi-objective topology optimization in AM. This involves simultaneously considering multiple physical phenomena (e.g., thermal, structural, and fluid dynamics) and objectives (e.g., weight reduction, strength, and cost) to generate optimized designs. The result is innovative structures that are lightweight, strong, and tailored to specific functional requirements. This approach is particularly beneficial for industries such as aerospace and automotive, where performance and efficiency are critical.
Lattice Structures: This theme explores the design and application of lattice structures in AM. Lattice structures offer significant advantages, including high strength-to-weight ratios and the ability to tailor mechanical properties through design. Research focuses on creating and optimizing lattice structures for various applications, from lightweight components in aerospace to porous implants in biomedical engineering. These structures can also be integrated with smart materials to develop multifunctional components for energy storage, thermal management, and other advanced applications.
DIGITALIZATION AND AUTOMATION
- Digital twin
- Data acquisition and handling to enable machining learning
- Build job set-up and simulation
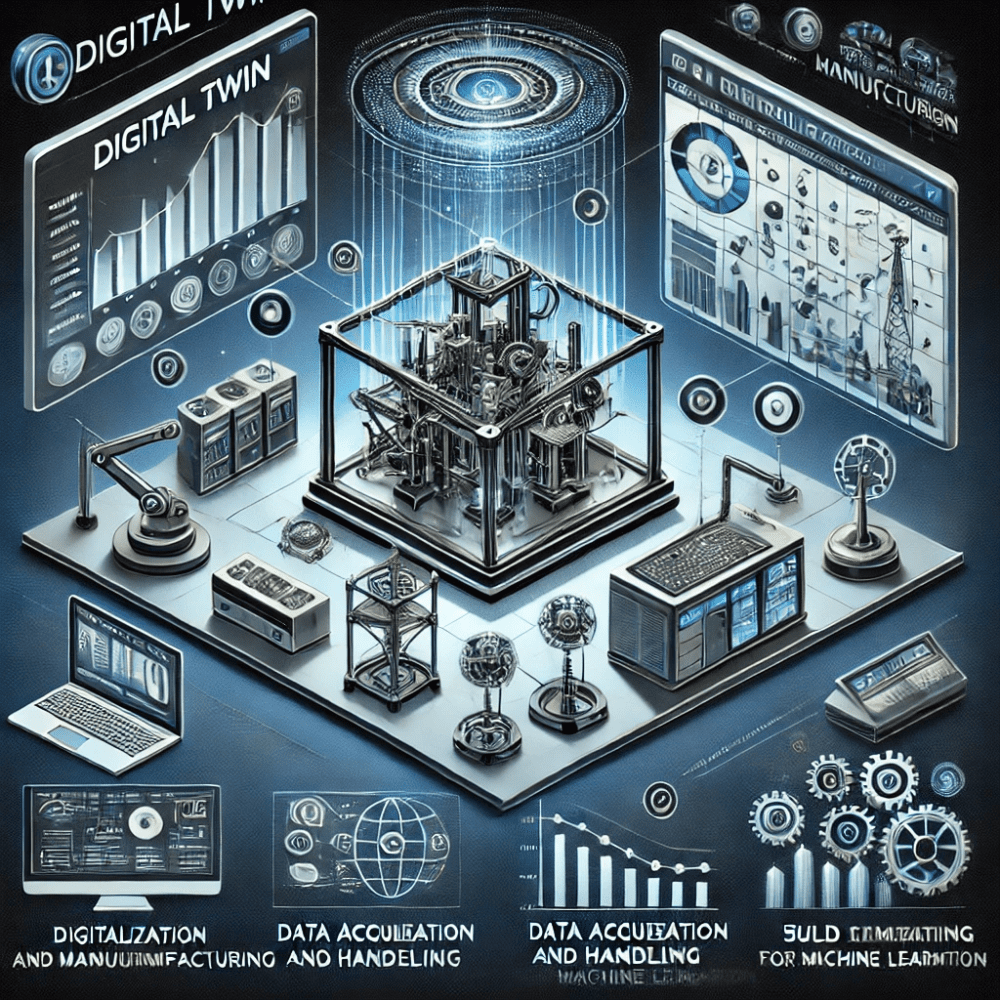
Digitalization and Automation
Digital Twin: Research in digital twin technology focuses on creating virtual replicas of physical additive manufacturing processes and systems. These digital models allow for real-time monitoring, analysis, and optimization, enabling predictive maintenance and process improvements. By simulating the entire manufacturing lifecycle, from design to production, digital twins enhance decision-making, reduce downtime, and improve overall process efficiency.
Data Acquisition and Handling to Enable Machine Learning: This theme involves developing robust systems for collecting, storing, and managing vast amounts of data generated during the additive manufacturing process. Advanced data acquisition techniques, including sensors and IoT devices, capture critical parameters in real time. This data is then processed and analyzed using machine learning algorithms to identify patterns, predict outcomes, and optimize manufacturing processes. The goal is to enhance the precision, reliability, and efficiency of additive manufacturing through data-driven insights.
Build Job Set-Up and Simulation: Research in build job set-up and simulation aims to streamline the preparation and execution of additive manufacturing jobs. This includes optimizing the orientation and layout of parts, generating support structures, and simulating the build process to predict and mitigate potential issues. By leveraging advanced simulation tools, researchers can ensure that each build job is executed with maximum efficiency and minimal risk of defects, ultimately improving the quality and consistency of manufactured parts
Machines and Manufacturing
- Post-Processing
- Laser Powder Bed/Fed Fusion and Binder Jetting
- Hybrid AM-Subtractive Process
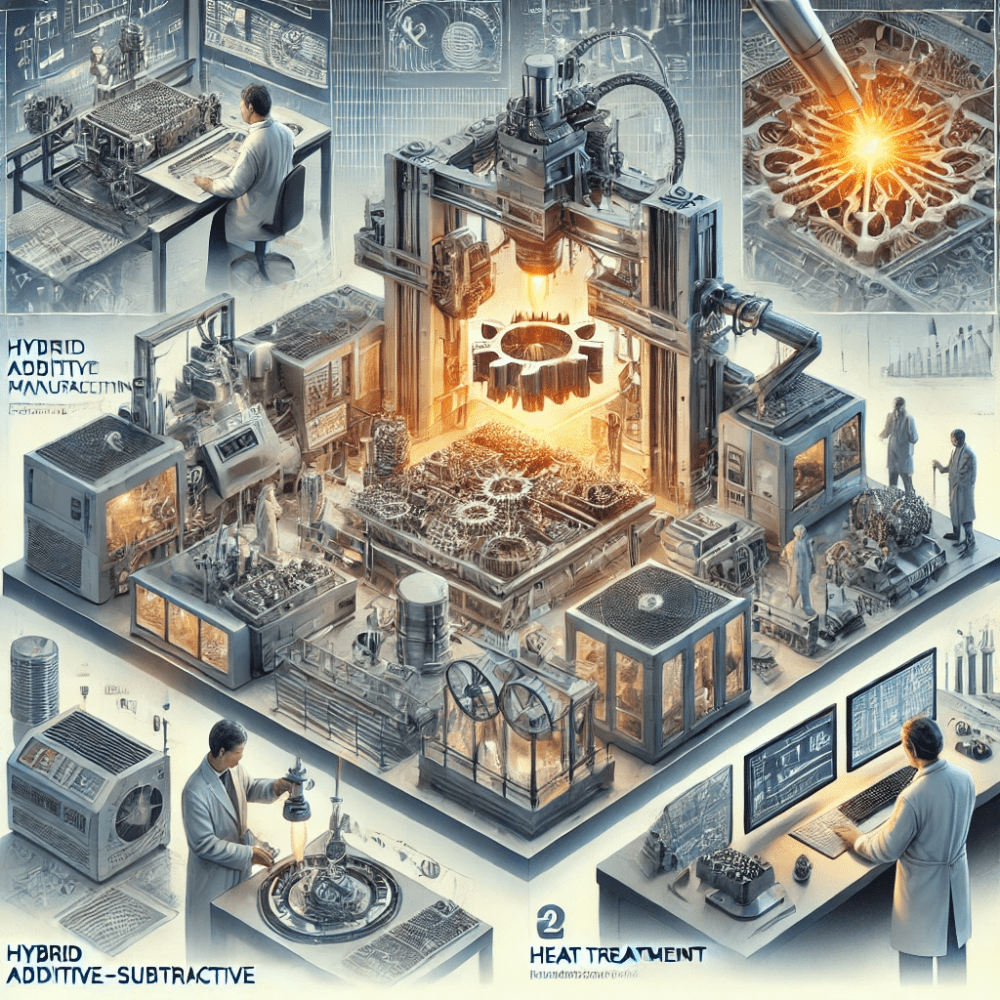
Machines and Manufacturing
Post-Processing: Advanced post-processing techniques are essential for refining the properties of additively manufactured parts. This research theme focuses on the development and optimization of post-processing methods such as heat treatment, surface polishing, and precision machining. These processes are designed to enhance mechanical strength, surface finish, and dimensional accuracy, ensuring that components meet the high standards required in industries such as aerospace, automotive, and biomedical.
Laser Powder Bed/Fed Fusion and Binder Jetting: Laser Powder Bed Fusion and binder jetting are key technologies in additive manufacturing. LPBF allows for the production of intricate geometries with high material integrity, making it ideal for high-performance applications in aerospace and energy sectors. Binder jetting, known for its scalability and cost-efficiency, is suitable for large-scale manufacturing. Research in this area aims to optimize process parameters, improve material utilization, and enhance the overall performance and reliability of these technologies.
Hybrid AM-Subtractive Process: The integration of additive and subtractive manufacturing processes offers a powerful approach to producing complex, high-quality parts. This theme explores the combination of additive manufacturing with traditional subtractive methods like milling and grinding. The hybrid approach enables the creation of intricate structures with excellent surface finishes and tight tolerances. Research efforts focus on developing smart materials and optimizing processes for applications in energy, automotive, aerospace, and biomedical fields, thus enhancing design flexibility, reducing production time, and improving part quality.